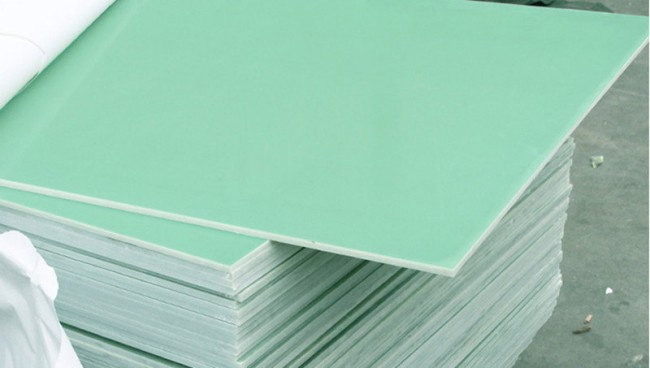
Modern electronics would not be what they are today without Printed Circuit Boards (PCBs).
These intricate boards, packed with microscopic pathways, serve as the foundation upon which countless devices are built. From smartphones and laptops to medical equipment and satellites, PCBs act as the invisible conductor, creating the flow of electricity that powers these marvels of technology.
When it comes to the many different materials that are used for the fabrication of PCBs, FR-4 is the most popular.
FR-4 material is used in a wide variety of electronic applications – it possesses a distinctive combination of properties. In order to gain a deeper comprehension of the reasons behind the widespread adoption of FR-4 in the PCB industry, this article will discuss its structure and properties.
Shall we begin our journey of discovery? Ler’s go!
FR-4: The flame-retardant workhorse
Just what does the abbreviation “FR-4” stand for? Here’s a clear explanation:
“FR” stands for “Flame Retardant,” and the number 4 represents a particular grade that falls under this overarching category. Flame retardancy is an essential characteristic that must be present in electronic components.
Let’s imagine that a short circuit is what causes a spark. Therefore, the properties of FR-4 help to ensure the safety and stability of electronic devices by preventing a spark from igniting into a full-blown fire.
Under the microscope with the ingredients of FR-4
The success of FR-4 depends on how cleverly it’s put together. Let us look at the important players:
- Epoxy resin: This acts as the glue that holds everything together. It’s a strong, lightweight polymer that boasts excellent electrical insulation properties, making it ideal for channeling electrical signals without leakage.
- Reinforcements: The backbone of FR-4’s strength comes from the reinforcements, typically woven fiberglass fabric. These glass fibers are incredibly strong and dimensionally stable, ensuring the PCB retains its shape. The weave pattern itself plays a role—a tighter weave joggers superior mechanical strength, while a looser weave provides better electrical performance through improved resin flow.
- Flame retardant additives: As the name suggests, these additives enhance FR-4’s ability to self-extinguish in case of fire. Common types include bromine-based compounds, but there’s ongoing research and development to explore more environmentally friendly alternatives due to potential environmental concerns.
- Optional additives: Depending on the desired properties, manufacturers might incorporate additional ingredients. Fillers like silica can be used to enhance thermal conductivity or improve fire resistance further.
Once these elements are combined, they undergo a high-pressure lamination process. Just picture it like this: a layer cake—the epoxy resin acts as the icing, sandwiched between layers of fiberglass fabric.
Heat and pressure are applied, fusing everything into a solid, reliable FR-4 sheet. This sheet then forms the foundation upon which intricate electronic circuits are built.
The properties of FR-4: The power behind its popularity
The dominance of FR-4 comes from more than just its ability to resist flames. Due to the fact that it possesses a winning combination of properties, it’s an excellent choice for a wide variety of electronic applications. For the purpose of establishing FR-4’s position as the PCB King, let us take a look at the key areas.
Mechanical marvel
Sturdiness, toughness, and dimensional stability are paramount for PCBs. Imagine a flimsy board—vibrations or physical stress could cause cracks, leading to circuit failure. FR-4’s glass fiber reinforcements provide exceptional strength and rigidity, ensuring the PCB maintains its shape under pressure.
The epoxy resin acts like a sturdy binder, further enhancing these mechanical properties. Also, FR-4 exhibits minimal dimensional change with temperature fluctuations, which is crucial for consistent performance across varying environments.
Balancing the electrical flow
For a PCB, efficiently transmitting electrical signals is its core function. Here, two key electrical properties come into play:
- Dielectric constant
- Loss tangent
The dielectric constant influences signal speed, while the loss tangent represents the energy lost during transmission. FR-4 strikes a remarkable balance. It offers a moderate dielectric constant, allowing for decent signal propagation speeds.
At the same time, its loss tangent is relatively low, minimizing signal degradation. It’s important to note that FR-4 is primarily an insulator, with minimal electrical conductivity – a desired trait for preventing unwanted current flow.
Keeping cool under pressure
Heat management is vital for electronic components. FR-4 demonstrates good thermal properties, meaning it can withstand moderate temperatures without compromising performance. The epoxy resin offers decent heat resistance, while the glass fibers help dissipate heat effectively.
While not the most thermally conductive material, FR-4’s thermal properties are sufficient for a wide range of electronic applications. In cases where high heat dissipation is critical, manufacturers might opt for alternative PCB materials with superior thermal conductivity.
Fabrication friendly
FR-3 shines in terms of its processing properties. It’s relatively easy to fabricate and machine, allowing for efficient PCB production. This translates to quicker turnaround times and potentially lower manufacturing costs.
The cost champion
Let’s not forget the economic factor. Compared to other PCB materials, FR-4 is a cost-effective option. This affordability, coupled with its versatility and well-rounded properties, makes it the go-to choice for a majority of electronic applications.
FR-4 vs. Rogers Material PCBs: When performance demands more
In spite of the fact that FR-4 regions are ideal for a wide variety of applications, there are situations in which even higher levels of performance are required. Rogers Materials come into play at this point.
In circumstances where FR-4 might not be adequate, these high-performance alternatives have been developed specifically for those circumstances. But what is the most important distinction?
Their ability to conduct electricity is what differentiates them from one another. Compared to FR-4, Rogers Materials has a dielectric constant and loss tangent that are significantly lower than those parameters.
Because of this, they are ideal for high-frequency applications such as RF circuits and communication equipment because they allow for faster signal transmission and minimal signal degradation. It does cost something, though, to have these greater electrical properties.
Rogers Materials are usually more expensive than FR-4 because they are made in more complicated ways and have different chemical makeups. Additionally, creating them might require more specialized techniques compared to creating FR-4, which is simple for everyone.
It comes down to the needs of your project and whether you should use FR-4 or Rogers Materials. If top-notch electrical performance at high frequencies is crucial, Rogers Material PCBs might be the superior option, despite the cost and processing considerations.
Applications of FR-4 – a marvel in action
The question now is, where exactly can we find these FR-4 marvels deployed in action? Take a look around you. It is highly likely that FR-4 is the secret sweet spot behind the scenes, whether it be the dependable smartphone you are holding in your hand or the laptop that is humming on your desk.
Due to the fact that it possesses a wide range of properties, it is the material of choice for a wide variety of consumer electronics, ranging from the intricate circuits that power smart TVs to the intricate components that compose gaming consoles. But FR-4’s reach extends far beyond our personal devices.
Industrial control systems that keep factories running smoothly and networking equipment that connects us all often rely on FR-4 PCBs for their reliable performance. Even medical devices, where precision and stability are paramount, can use FR-4 for certain components.
And that’s just the tip of the iceberg—countless other electronic devices, from simple toys to sophisticated scientific instruments, silently depend on this versatile material.
FR-4’s ability to strike a balance between cost, performance, and ease of use makes it the workhorse material powering the modern electronic world.
Use the power of FR-4
The fact that FR-4 went from being a straightforward mixture of epoxy resin and fiber glass to becoming the preeminent material used in the fabrication of printed circuit boards is evidence of the remarkable properties it possesses.
Through our investigation of its ingenious composition, we have brought to light the role that each component plays in the production of a sturdy and dependable material.
From its remarkable mechanical strength and balanced electrical performance to its thermal stability and user-friendly processing, this material has a lot going for it.
FR-4 offers a winning combination that’s hard to beat. Despite the fact that there are alternatives, like Rogers Material, that offer higher performance, FR-4 has established itself as the undisputed workhorse material in the world of PCBs due to its low price and flexibility.
Therefore, the next time you turn on your preferred electronic device, make sure to take a moment to appreciate the unsung hero that is hiding beneath the surface: the ubiquitous FR-4.
Also Read: