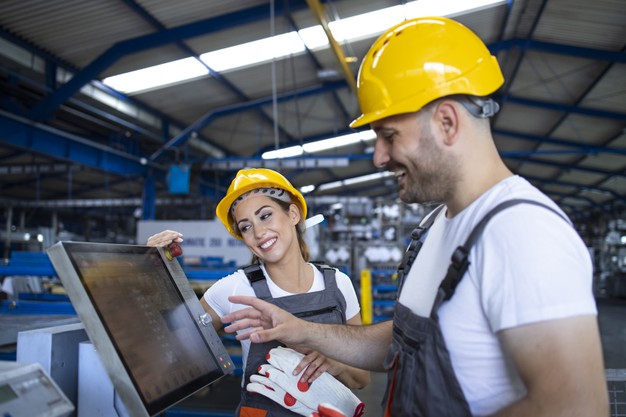
The backbone of every industrial unit is maintenance. Without proper maintenance, a plant cannot operate smoothly. Well-planned maintenance activities can raise the quality standards of your productivity and give you a competitive edge over others.
Additionally, maintenance plays a critical role in controlling the overall cost of running the unit. Beyond just preventing breakdowns, maintenance also ensures that the equipment is optimally used to produce high-quality goods.
The Essence of Maintenance Management in Manufacturing
Optimal Maintenance Management directly influences quality control and operational consistency. Manufactured items must meet precise standards to retain customer trust.
Lack of structured upkeep leads to equipment deterioration, erratic production schedules, and unexpected expenses. A well-organized program focuses on identifying potential failure points, organizing routine servicing, and keeping production lines at peak efficiency.
Key Points to Remember
- Maintenance fosters cost savings over the entire equipment lifespan.
- Preventive measures help detect issues before they escalate.
- Engaging in periodic inspections protects against safety hazards.
- Scheduled downtime reduces random breakdowns and improves worker morale.
Leaders treat Maintenance Management as a method to reduce overall production costs while sustaining dependable workflows.
Machinery that runs consistently often generates higher output, leading to better profit margins. In a competitive setting, consistent product delivery differentiates top performers from those with frequent setbacks.
Key Benefits of Structured Maintenance Management
- Longer Equipment Lifespans: Sustaining machines through planned activities and timely repairs yields longer operational periods. Equipment is an expensive asset, so proper maintenance prolongs the interval between costly replacements. Investing in upkeep prevents small defects from turning into larger complications.
- Reduced Unexpected Downtime: Unscheduled halts typically carry hefty financial penalties. Maintenance Management reduces the likelihood of abrupt malfunctions by scheduling repairs at optimal intervals. Careful planning limits disruptions, ensuring production lines keep churning out goods. Proactive steps guard against frantic troubleshooting.
- Enhanced Safety Conditions: Machinery failures can compromise workforce well-being. Routine assessments uncover possible hazards before they cause injuries. Well-maintained equipment lowers the risk of fires, leaks, or malfunctions that may endanger personnel. Organizations often prioritize safety to comply with regulations and protect brand image.
- Consistent Product Quality: Maintenance correlates with stable performance. Worn parts can cause errors in product calibration or packaging, resulting in inconsistent outputs. Precise service routines tighten controls, enabling consistent item specifications. An orderly environment also boosts confidence among buyers who appreciate products with uniform quality.
- Optimal Use of Resources: By preventing equipment from losing efficiency, maintenance contributes to higher throughput with lower waste. Higher overall yield can minimize production costs while meeting demand. Energy consumption levels also tend to be lower when tools function as designed, which supports environmental responsibility.
Types of Maintenance Strategies in Manufacturing
Varying approaches exist for Maintenance Management. Each methodology offers unique strengths, and selecting the most suitable strategy involves analyzing equipment characteristics, operational demands, and financial resources.
- Preventive Maintenance: Maintenance tasks occur at set intervals, whether or not a problem has presented itself. Manufacturers rely on schedules based on calendar dates or machine running hours. This approach lowers the chance of failure, although it could mean servicing parts that might still have life left in them.
- Predictive Maintenance: Sensor data and performance insights predict when a component will fail. Advanced monitoring tools analyze parameters such as vibration, temperature, and noise levels to identify possible risks. Repairs or replacements are timed just before the expected breakdown, saving time and money. This method leans heavily on technology and data analytics.
- Reactive Maintenance: Repairs happen only after equipment ceases functioning. Some organizations consider it an acceptable approach for low-priority or easily replaceable items. However, relying too heavily on reactive steps often leads to higher long-term costs and unexpected standstills.
- Condition-Based Maintenance: Actual conditions guide the frequency of service. Technicians watch for specific signs of deterioration, such as increased temperature or slower performance, then take timely measures. This strategy seeks to combine efficiency with cost-effectiveness.
- Total Productive Maintenance (TPM): TPM promotes a culture where everyone from technicians to operators contributes to equipment care. Employees track machine health to identify warning signs early on. This collective effort can streamline processes and encourage consistent improvement.
Best Practices and Effective Implementation
1. Comprehensive Maintenance Scheduling
Plant managers often rely on sophisticated tools to plan tasks. Digital calendars and specialized software simplify the process, ensuring no task slips through the cracks. Organized routines keep the workforce synchronized and minimize oversight.
2. Standard Operating Procedures (SOPs)
Clear protocols guide each step, from inspection to final checks. SOPs clarify responsibilities and reduce confusion among staff. Well-defined instructions raise the bar on quality and reinforce consistency across shifts.
3. Worker Training and Skills Development
Talented professionals bring an edge in Maintenance Management. Technicians must learn how to troubleshoot complex assemblies and interpret sensor output. Updated training keeps teams prepared for evolving challenges. Investing in education leads to fewer errors and shorter repair times.
4. Accurate Documentation
Records of repairs, parts replacements, and operational history allow easy identification of patterns. Data insights reveal recurring faults, guiding prevention strategies and improving decision-making. Documentation also ensures regulatory compliance in sectors governed by strict safety rules.
5. Up-to-Date Inventory Management
No one wants a production delay caused by missing replacement parts. Maintaining a well-stocked inventory of critical items saves time during repair tasks. A balanced approach ensures a continuous supply without overstocking, which can tie up capital unnecessarily.
6. Emphasis on Quality Assurance
Spot checks validate that new parts meet specified standards. Subpar components can sabotage the best maintenance efforts. Thorough quality assurance extends machine life and boosts operational stability. High-grade materials often pay for themselves by preserving operational flow.
7. Regular Audits and Continuous Improvement
Performance metrics such as Mean Time Between Failures (MTBF) and Mean Time To Repair (MTTR) spotlight strengths and weaknesses. Audits shed light on any gaps in coverage, prompting updates to schedules or processes. Continuous improvement fosters a forward-thinking culture that encourages better outcomes.
The Impact of Technology on Maintenance Management
1. Real-Time Monitoring: State-of-the-art sensors capture operational data around the clock. Instant alerts notify engineers when values deviate from normal ranges. Speedy intervention can head off serious breakdowns. Real-time tracking helps managers schedule service activities more efficiently, limiting downtime.
2. Data-Driven Insights: Software platforms crunch huge amounts of data to identify early warning signs. By studying temperature trends or unusual vibrations, professionals can hone in on root causes. Statistical models reveal hidden flaws, refining plans for future improvements. Those who leverage data insights stand a higher chance of staying competitive.
3. Augmented Reality (AR) Tools: Technicians can access virtual overlays that highlight machine components, step-by-step procedures, or recommended actions. AR reduces guesswork, shortens training time, and ensures consistent quality, particularly when equipment has multiple intricate parts. Instructional visuals lower the risk of human error.
4. Artificial Intelligence and Machine Learning: AI engines can interpret historical data to predict emerging faults. Automated pattern recognition enables quick adjustments to maintenance schedules. Machine learning algorithms adapt to changes in equipment usage or production environments, adding flexibility and resilience. This technology transforms raw data into actionable guidelines.
5. Cloud-Based Collaboration: Cloud systems store documents, procedures, and analytics in secure online environments. Stakeholders access real-time logs, share updates, and coordinate tasks seamlessly. Remote oversight benefits teams managing multiple sites, or those who need quick updates without on-site visits. Transparency across departments cements an organized approach.
Common Challenges in Maintenance Management
- Limited Budget Allocation: Tight budgets sometimes compel organizations to postpone upgrades, rely on outdated machinery, or skip crucial inspections. Over time, such decisions often create bigger problems. Financial planning should include dedicated funds for long-term machine upkeep.
- Inaccurate Data Interpretation: Data overload can be daunting, especially for teams lacking training in analytics. Misinterpreting trends can steer maintenance decisions in the wrong direction. Investments in user-friendly interfaces and staff education help clear these hurdles.
- Communication Gaps: Miscommunication between production and maintenance departments causes confusion and delays. Clear guidelines and shared objectives promote alignment. Status updates and daily meetings help ensure each group understands scheduled tasks and upcoming needs.
- Resistance to Change: Shifting from reactive to proactive methods might meet internal resistance. Some employees prefer to continue with familiar routines. Gradual training, transparent discussions about benefits, and celebrating initial successes can drive cultural transformation.
- Skill Shortages: Industry leaders often face difficulty finding individuals with in-depth knowledge of machinery, electronics, and analytics. Expertise is crucial for diagnosing subtle problems. Hiring and retaining skilled personnel ensures seamless coverage for planned and unplanned events.
Deeper Insights on Maintenance Metrics and Performance Tracking
A thorough strategy often includes measurement and ongoing evaluation. Key metrics like Overall Equipment Effectiveness (OEE), MTBF, and MTTR help teams gauge progress.
OEE bundles availability, performance, and quality into one figure, allowing managers to see how efficiently operations run. Evaluating each dimension can reveal the root source of inefficiencies. Over time, incremental gains in these values translate into significant boosts for production lines.
In many plants, an 80% OEE target might indicate strong performance. A closer look at the data points can highlight whether the limiting factor is frequent downtime, slow throughput, or product rejections.
Such visibility encourages a methodical approach to improvement. Tracking and documenting daily data also spurs accountability among maintenance crews.
Risk Management and Predictive Trends
Manufacturing organizations must anticipate operational risks. Machines that process intense workloads encounter more wear and tear, making forward-thinking planning indispensable.
Early warning signs such as minor vibrations, noisy bearings, or unexpected temperature spikes are typically detected before major disruption occurs. Diagnostic tools help experts examine anomalies and arrange timely repairs. Putting these methods in place leads to safer, more efficient production cycles.
Industry trends hint that sensor-driven and AI-assisted maintenance will gain further traction. Over time, data collection and analytics capabilities will evolve, allowing narrower maintenance windows and fewer guesswork-based decisions.
New sensor technologies likely will measure subtle shifts in performance that were previously undetectable. Adapting to these advances places organizations on a path toward near-perfect uptime.
Cost Control and Resource Allocation
Maintenance Management provides a structured framework for managing expenses. Uniform checks and well-coordinated repairs eliminate the panic that often arises during emergency shutdowns.
Bulk purchasing of spare parts, negotiated vendor contracts, and systematic scheduling of replacements can lead to considerable savings. The art of balancing cost with readiness stands as a guiding principle.
Cost-benefit evaluations that measure lost production time against the price of maintenance initiatives often shine a spotlight on the long-term gains. Skimping on proactive measures initially seems like a way to save money, but that decision can morph into a hefty invoice if critical equipment grinds to a halt.
Cutting corners on essential services might shave a few dollars in the short term, yet the bigger risk includes lasting reputational harm when orders can’t be fulfilled on time.
Embracing a Culture of Continuous Learning
Organizations that treat Maintenance Management as a living process often see results. There is no final endpoint because machinery, technology, and people change over time. Best practices that served well five years ago may appear outdated when new production methods or digital tools enter the scene.
Emphasizing incremental refinements allows teams to stay engaged. Quality circles or cross-functional committees often share lessons gleaned from each round of improvements.
Mentorship programs can also support skill growth among new staff members. Seasoned technicians impart practical knowledge that extends beyond manuals, which strengthens future operations.
In many factories, a sense of collective responsibility emerges from focusing on consistent machine health, reinforcing a spirit of collaboration.
Conclusion
Maintenance Management in manufacturing fosters longer machine lifespans, safer conditions, and predictable output. Thoughtful planning includes preventive or predictive approaches tailored to each piece of equipment.
Tracking metrics and leveraging technology bolsters outcomes and identifies hidden trouble spots. Proper funds, skilled personnel, and effective processes keep machinery humming, enabling steady production and strong financial performance.
Any organization that invests time and effort in these methods gains an edge by mitigating risks and satisfying market demands.
FAQs
Q1: Why is Maintenance Management essential for manufacturing?
Sound upkeep of manufacturing assets supports continuous productivity and reduces sudden halts. It also promotes safety and helps maintain consistent quality standards that satisfy consumer demands.
Q2: Which maintenance strategy is best for complex machinery?
Predictive Maintenance often excels for machinery with expensive parts and sensitive instruments. Live sensor data pinpoints abnormalities early, preventing extensive damage and cutting operational disruptions.
Q3: How does proper maintenance improve bottom-line results?
Minimized downtime lowers operational costs. Quality remains more stable when equipment is healthy, elevating brand image and boosting customer loyalty. Well-maintained systems often deliver higher output, further impacting profitability.
Q4: Is Reactive Maintenance ever acceptable?
It might be an option for non-critical machinery, such as backup devices or tools with low replacement costs. However, relying too much on reactive measures can trigger significant setbacks if high-priority systems fail.
Q5: What role does technology play in Maintenance Management?
Sensors, AI, and analytics uncover patterns and forecast potential breakdowns with precision. Real-time monitoring devices provide immediate feedback, enabling quick responses that guard against large-scale malfunctions.
Q6: How can manufacturers secure sufficient funding for maintenance initiatives?
Decision-makers often present cost-benefit analyses that underscore the savings from avoiding downtime and extending the life of equipment. Illustrating potential losses from breakdowns helps justify continuous support for maintenance budgets.
Q7: How frequently should equipment undergo preventive checks?
Interval lengths vary based on machine usage, manufacturer recommendations, and historical breakdown data. Some organizations link maintenance intervals to operational hours, while others use monthly or quarterly schedules.
Also Read: