Micro services enable the micro-precision machining industry’s quick growth. New improvements or machining techniques can be easily added into the precision machining technology as they are being developed.
In this case, a new scheduling of maintenance algorithm can be tested and put into effect in high-precision machining without first affecting different services.
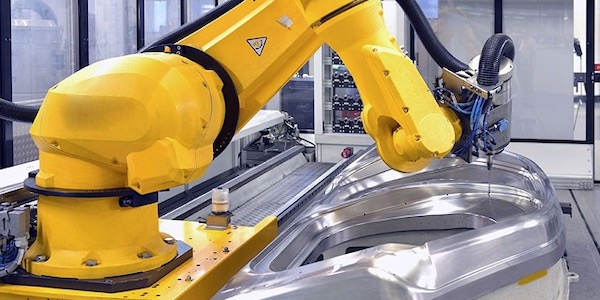
Microservices and IoT devices may be easily connected thanks to micro precision machining, particularly is becoming increasingly frequent in modern machining process setups.
Each device, instrument or piece of equipment can interface with a specific microservice, ensuring precise information and quick evaluation.
When performing complex machining services, continuous input from machines and instruments can result in more accurate and efficient procedures.
In this article, we will discuss on Microservices and their capabilities for bettering high-quality machining services.
Enhancing Precision in CNC Machining with Microservices
The microservices-based digital replica platform for high precision machining service modules consists of the following elements: data collection, storage spaces, calculation, exchange, invocation, presentation along with every other relevant issue.
The information gathering segment usually receives information obtained from data gathering devices, also obtains data production shop functional signals via CNC precision machining services, and needs to have both end-to-end data read/write capabilities as well as data storage structure.
The gathering of data devices encompasses sensors and tags with RFID chips and audience members, computerized signal processing equipment.
Also additional tools for measuring the force needed for cutting, torque, speed, acoustic emissions and the environment, etc. on precision machined parts.
The CNC system of the machine tool serves as the basis for the machine tool connection. This uses protocols like OPC-UA and MTConnect to collect data like the consuming axis dimensions that show the velocity, load, along with danger signaling of the production tool.
The information collected by the sensors from the equipment being used and the information obtained from the findings of the simulation are both utilized further by the computer’s algorithm component.
By merging various types of algorithms to find data features, eliminate disturbance in information or appraise frameworks, it assesses the true meaning behind the data as well as pinpoints the source of problems.
The algorithm module of a digital twin system works like the brain, absorbing enormous amounts of data rapidly and efficiently. In addition to the communication module of the twin computer system showing the results, it further improves the accuracy of the high-precision machining model.
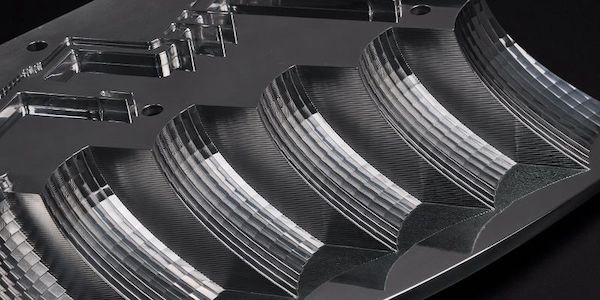
The creation of digital replicas provides answers to the challenging issues connected to complex machining services.
The computational technological assessment component for the twin platform was created to make it possible to look at problems from different perspectives while employing the understanding base’s assessment requirements.
It may also give assessment the results; lead the development of globally ideal processing equipment improvement plans. This conducts optimization procedures for specific analyzing plans, and comprehensively evaluates numerous assessment strategies for a particular operating area.
The procedure improvement generator for machining procedures is in charge of simplifying the machine operation by altering the working parameters, tool routes, tool placements, and tool entrances.
It is also responsible for selecting the optimal tools in accordance with the results of the analysis module’s observations. The evaluation from the previous lesson is expanded upon, and any areas where the appropriate manufacturing standards are not met are attempted to be corrected.
Invisible numerical control INC-based schemes
The core element of the producing structure that governs precision machining services is the CNC system. As computer/information innovations improve swiftly, it is essential to get the most from the development and use of CNC in order to boost machining precision along with throughput, while decreasing machining costs.
One of the modern manufacturing principles, known as “Industry 4.0,” promises to increase adaptation, through networked environments in order to accelerate up production, cut costs, and increase versatility of systems.
Even while the top layers of industrial systems are evolving approaching cloud computing along with a service-centered approach, CNC systems are still limited to local equipment.
Modern CNC precision machining is unable to function on remote platforms due to the tightly connected architecture of CNC systems. Important tasks like tool route extensions and machining software understanding are carried out by lesser systems that operate continuously.
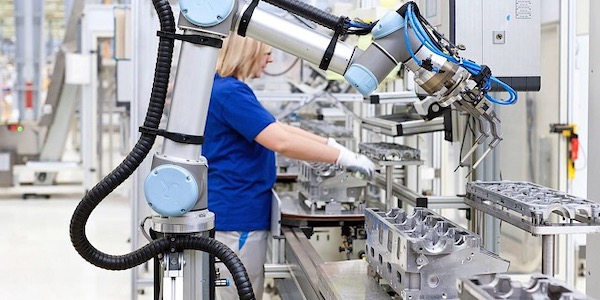
These kinds of systems require real-time performance; hence CNC function procedures must be built correctly. These capabilities can only be used to service the matching local computer. The more functionality that is added to the existing CNC design, the less reusable its possibilities become.
An innovative sort of organization is INC, or imperceptible mathematical oversight. The INC system is arranged in a way that is not tightly linked and takes advantage of standard technological advancements.
By using “object-oriented programming (OOP)” and “service-oriented architecture (SOA)” methodologies, Ethernet connections’ capacity is expanding swiftly, along with storage capacity.
For precision machined parts, the INC framework provides non-real-time machine operator messages.
Using the use of loosely connected frameworks and the design that establishes connectors between function sections to INC accomplishes an unparalleled level of growing its presence, and overall performance flexibility. The INC system is plug-and-play compatible with all types of machine tools.
As a consequence, INC is able to function remotely as opposed to installing CNC equipment domestically. This attribute is essential for achieving high levels of configurability, capacity, and functional adaptability.
Microservice architectures and decision support in precision machining
The complexity of models and processes that make projections and ultimately aid when making choices makes it more difficult to create transparency structures.
Fuzzy Cognitive Maps (FCMs), which combine logic that is fuzzy and neural networks as their components, are soft instruments for dealing with intelligence in computation.
FCMs have gotten a growing amount of attention ever since they were initially brought up in the scientific literature.
The Activation Levels Genetically Evolved Multi-Layer Fuzzy Cognitive Map (ALGE-MLFCM) microservice framework is at the center of a new Decision and Evaluation model of the critical factors to consider when implementing a microservice framework.
The proposed model enables investigation and evaluation of those crucial characteristics, and their influence and interrelation, by means of a variety of distinct procedures and an efficient interpretive approach.
Conclusion
Despite the buzz regarding microservices, neither business nor academia can agree on the perfect conditions required to embrace and benefit from this novel strategy.
The majority of companies are not equipped to fully utilize microservices because they are dependent on within the premises application structures. along with transferring to this the atmosphere is not a simple task considering the fact that these patterns are incredibly multifaceted and encompass numerous, often diametrically opposed components.
Furthermore, businesses who are thinking about deploying microservices from scratch run the risk of being required to pay more for them, thereby increasing the complexity and expenses when it wasn’t strictly essential given the needs of the structure that was under construction.
The decision to use microservices, perhaps to transfer a previous monolithic system or to build an entirely new one from the decision to use microservices, perhaps to transfer a previous monolithic system or to build an entirely new one from start is therefore crucially important for numerous parties involved to studies and examine.
The decision to use microservices, perhaps to transfer a previous monolithic system or to build an entirely new one from the start, is therefore crucially important for numerous parties involved to study and examine.